
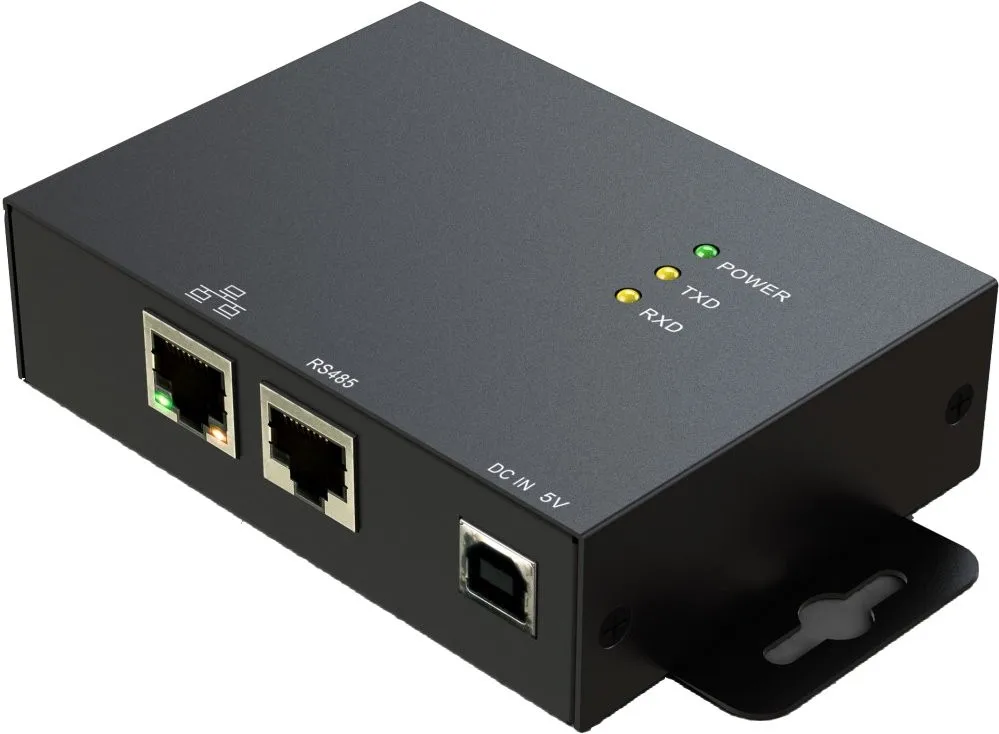
- #MODBUS SERVER AND DEVICE NOT COMMUNICATING HOW TO#
- #MODBUS SERVER AND DEVICE NOT COMMUNICATING SERIAL#
- #MODBUS SERVER AND DEVICE NOT COMMUNICATING DRIVERS#
#MODBUS SERVER AND DEVICE NOT COMMUNICATING HOW TO#
It is an open-source package (or library) developed for several languages, such as VB, C++, Java, Python.etc, which allows us to communicate inherently via the S7 protocol (GET/PUT access).In this tutorial, you will learn how to use Snap7 to communicate with an S7 PLC. It has never been easier to communicate with PLCs or other industrial devices.If you wantwould like to develop a solution to communicate with a Siemens PLC, Snap7 is the ideal tool. Their adoption offers great flexibility when choosing equipment and dramatically facilitates communication between several different devices. The Mesh-enabled unit features local configuration, scan & configuration, and diagnostic tools otherwise only available in the AcuMesh setup software.Industrial Ethernet and other TCP communication protocols have become a standard in the industry. AcuLink 810 has the ability to communicate directly with AcuMesh devices using either an 868MHz or 900MHz channel. The built-in Mesh features create a user-friendly setup and troubleshooting process with all information located on a single platform.
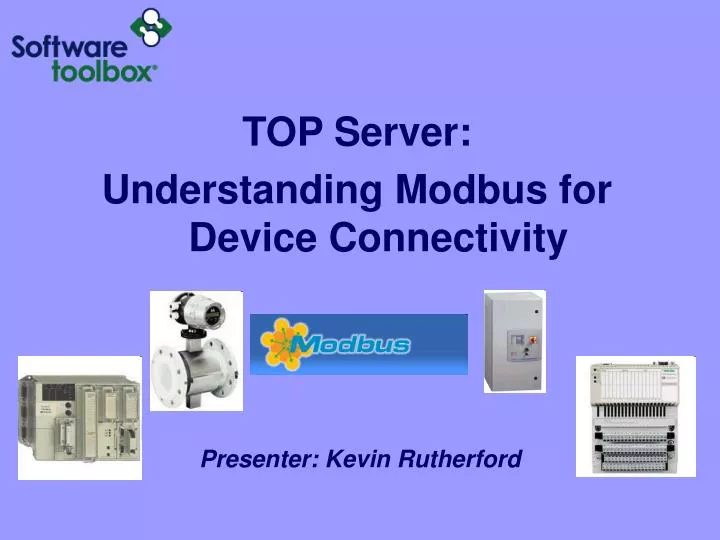
It is able to communicate using the Modbus protocol. Wireless Modbus and Accuenergy The AcuLink 810-900 and AcuLink 810-868 data acquisition device can be transformed into a wireless master in a standalone network by polling connected electronic devices and store the data either internally, post to software, or server. Simultaneous support for Ethernet, RS485 and RS232.Support for multiple Modbus options – RTU and TCP/IP.
#MODBUS SERVER AND DEVICE NOT COMMUNICATING SERIAL#
Ethernet, unlike serial communication, sends data via packets over a TCP/IP network. Modbus TCP/IP runs on the Ethernet over the TCP interface transport layer utilizing the improvements in speed and number of connected devices. Slave devices do not communicate with other slave devices. Modbus RTU does this through a serial communication protocol that sends binary data (1 and 0) sequentially from the master and slave. Master devices such as DAQs poll field sensors and meters by sending a request to receive a status response at regular intervals. It uses a Master/Slave configuration to communicate between devices. Difference Modbus RTU (RS495 and RS232) is still the most commonly used implementation in industrial automation due to cost and practicality. RS485 standard is often used in a master-slave arrangement- when one device, the master, initiates all communications activity, and controls the slave devices connected to it.
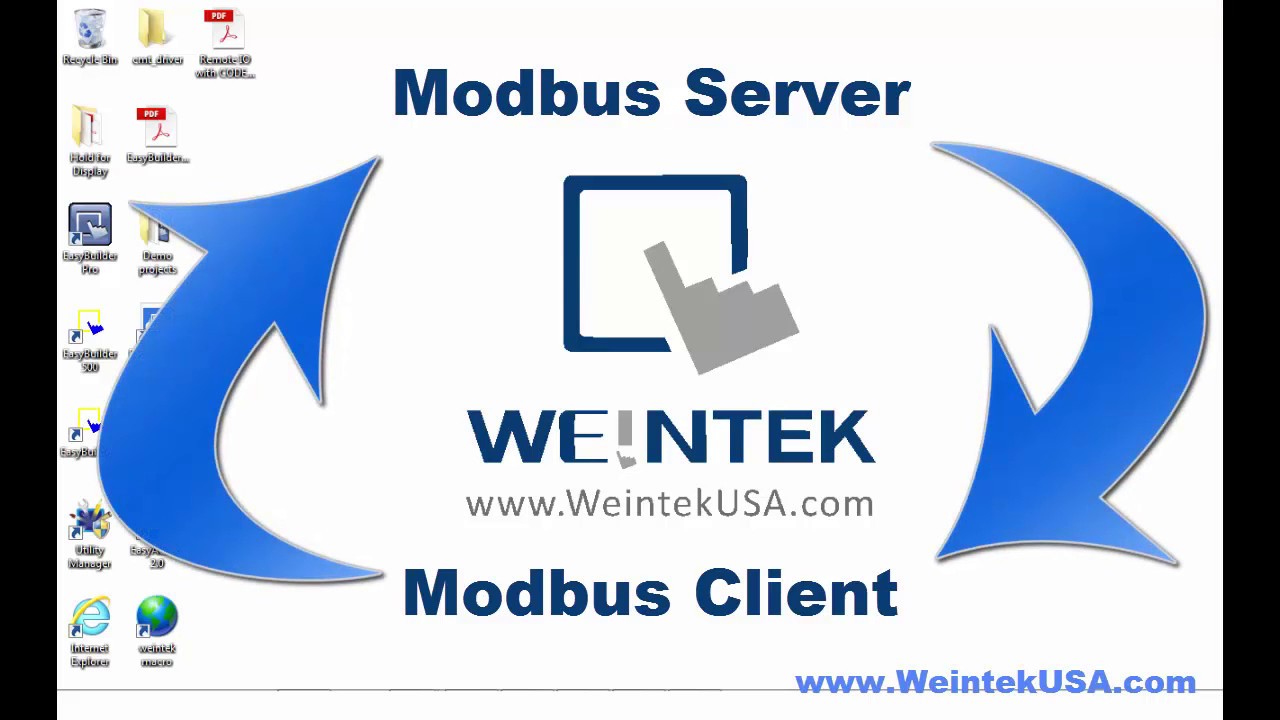
This standard is commonly used in commercial buildings and industrial environment for energy management and building automation applications because it can be used effectively over long distance and electrically noisy environments.
#MODBUS SERVER AND DEVICE NOT COMMUNICATING DRIVERS#
RS485 is a standard defining the electrical characteristics of drivers and receivers for use in serial communication systems. This can be designed for any type of Modbus including two of the most common options – TCP/IP and RTU. Wireless Modbus provides an added layer enabling Modbus devices to transmit information wirelessly. Modbus is a serial communication protocol on the application layer used to transmit data between electronic devices used in the industrial automation and control industry.
